Hot-Dip Galvanizing (Substance) VS Powder Coat or Paint (Style)
One of the most surprising issues PT&P has run into in its 1000+ audits of operating plants is corrosion due to the use of Paint or Powder Coat Systems for corrosion protection. As with most things in life, you can not have your cake and eat it too. Paint can be very attractive.
However, the attractiveness comes at a price…
![]() |
Figure 1 – Pictures of New Galvanized Pipe and Painted Steel Pipe
|
Figure 2 – Pictures of 25-Year-Old HDG Support VS. 8-Year-Old Painted Support
![]() |
![]() |
PT&P Hot-dipped Galvanized Support 25 Years In-Service in Dubai – Salt Air from Persian Gulf – 100 Sandstorms per Year |
NON-PT&P Painted Support 8 Years In-Service in Texas Salt Air From Gulf Coast |
The other primary advantage of paint is that it works better with very thin gauge steel. Thin gauge steel will warp under the heat of the hot-dip galvanizing process. Obviously, the combination of thin gauge steel and paint for corrosion resistance will lead to a shorter service life; however, it provides an advantage in terms of cost reduction due to weight savings.
![]() |
![]() |
PT&P Hot-dipped Galvanized Support 25 Years In-Service |
NON-PT&P Painted Support 8 Years In-Service in Louisiana |
The most fundamental difference between the 2 types of surface protection is summarized below:
Painting is a Coating – Paint or powder coating in its various forms is just simply a coating. It does no more than adhere to the underlying steel as you would expect from substances such as epoxy or acrylic which can not bond with Steel. As a result, it is much easier to achieve a uniform finish that is unrelated to underlying Steel.
Hot-Dip Galvanizing Involves a Chemical Reaction – HDG is much more than a coating. The process creates a chemical reaction that bonds the zinc and steel together to the point where electrons are moved from the zinc to the steel as part of the protection process. Because there is a chemical reaction, it is more challenging to achieve the same level of cosmetics as paint but it does provide a far superior level of protection.
Figure 3 – Picture of Thin Gauge Steel Better Suited to Painting
Any coating which provides a barrier to the moisture and oxygen in the air will help protect carbon steel from corrosion. A properly painted surface will provide a barrier, but it is subject to scratching from contact with hard objects.
Figure 4 – Illustrates how rust can grow and damage a painted surface when corrosion begins because the paint barrier is broken by a scratch.
Figure 5 – HDG vs Organic Coatings (from German Technical Presentation)
Source: Conference Paper on Galvanizing of highway and railway bridge constructions for Dynamic Loads (Germany) by M.Oechsner Technische Universität Darmstadt, Fabrian Simonsen EJOT Tambach GmbH, Dieter Ungermann Technische Universität Dortmund, Dennis Rademacher ArcelorMittal Europe.
Figure 6 indicates how corrosion damages carbon steel. Note that the pitted area to the right is anodic and gives up electrons while the cathodic area to the left (where water and oxygen from the air are present) is where rust appears. The pitted area where the carbon steel is weakened is not where the rust appears.
Zinc has a greater tendency to give up electrons than carbon steel, so when both are present, zinc becomes the anode and protects the carbon steel.
Figure 7 indicates corrosion with the zinc giving up the electrons and becoming pitted while the carbon steel remains undamaged. From this, we see that a zinc coating will protect carbon steel by “sacrificing” itself until the zinc is depleted. The rate of zinc depletion is relatively slow when the pH of the electrolyte is between 4 and 13.
HDG Corrosion Benefits
The following are the benefits of HDG for Corrosion Protection:
Abrasion Resistance – HDG is not one layer of coating but actually 4 layers of coating with different properties and different combinations of zinc and steel. The top layer is 100% Zn with a 70 DPN harness. Each layer closer to the base steel has an increasing level of hardness all the way to the Gamma Layer which is 75%Zn, 25% Fe and has a hardness of 250 DPN which is harder than the base steel which has a 159 DPN hardness.
Figure 8 – Layers of Hot-Dip Galvanizing and Associated Hardness
Cathodic Protection – A protection aspect of HDG that cannot be replicated with a simple coating such as Paint is the Cathodic protection of Zinc. Salt water acts as an electrolyte between zinc and steel in an electrochemical circuit with zinc acting as the anode and steel as the cathode. As a result, steel is protected from corrosion until the Zinc is fully consumed. This means even exposed steel will be protected from corrosion by the zinc around the steel. Cathodic protection is important enough to be required on some Piping systems by Federal code.
Figure 9 – Cathodic Protection of HDG VS Paint
Below are examples of a painted pipe support with initial corrosion due to lacking cathodic protection, and a picture of deterioration once the initial corrosion has taken hold. As you can see, any pinhole, scratch, or nick will set off a corrosion process. Our experience has been from the time of manufacture, many areas are vulnerable to some damage to the surface coat during either construction or post turnover. This is devastating for a painted finish.
Figure 10 – Real World Example of Paint and Lack of Cathodic Protection
At Piping Technology and Products Inc., many customers have returned painted variable and constant spring supports which could no longer function due to corrosion. Costs must be considered during the specification of coatings for pipe supports. The owner and operator of a facility should consider life-cycle costs. Pipe supports are usually a relatively small percentage of the total cost of installing and operating a power plant, petrochemical plant, paper mill or other major facility. The small additional cost of hot-dip galvanizing the carbon steel components of pipe supports is most always a wise investment.
Figure 11 – Real World Examples of HDG VS. Paint / Lack of Cathodic Protection
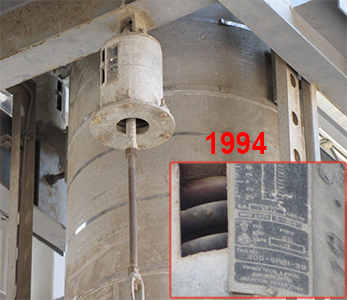
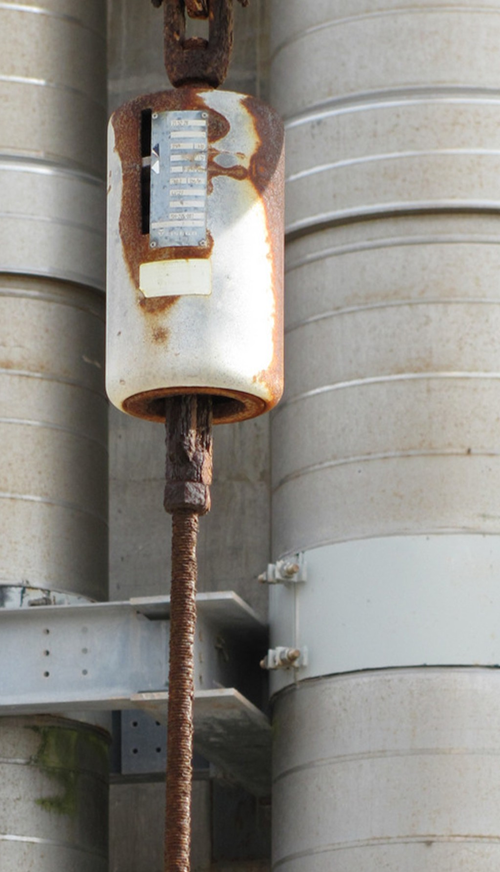
Zinc Patina – As Zinc is initially exposed to moisture, it reacts with water to form a porous layer of Zinc Hydroxide. As the material dries, it converts to a thin layer of Zinc Carbonate that is a passive, stable film that is not water soluble. The process of Zinc Patina formation takes approximately 6-12 months from the time of hot-dip galvanizing. This layer of zinc patina turns matte gray in color and significantly slows the rate of corrosion. The Zinc Patina is one of the reasons that the Salt Spray test is a very poor indicator of the benefit of galvanizing as keeping galvanized material wet does not allow for the formation of Zinc Patina.
Figure 12 – Formation of Water Insoluble Zinc Carbonate Surface Layer
Summary
Hot-dip galvanizing is almost always the superior solution for corrosion protection of structural steel. The cases in which paint can be useful include working with thin gauge material (which cannot withstand the heat of HDG processing without warping), or situations in which the cosmetics of painting is of high value.
If you have a significant number of painted structural steel elements in your plant that are having corrosion issues, please call Piping Technology and Products. We have seen this issue in a surprising number of plants, and we can develop a strategy for moving to a more resilient corrosion prevention approach.