PT&P has found that many of its customers do not optimize designs with superior material choices. There are many reasons for this. One of the biggest is that many steel fabricators serving operating plants and EPCs are limited in both their engineering and manufacturing capabilities. They fall into working only with the basics such as A36 and 304 Stainless. As the only global provider of engineered supports and expansion joints, PT&P works with an extraordinarily broad range of materials including high-strength steel, a full range of stainless steel, superalloys, thermoplastics, and insulation and isolation materials. View our product archives for PT&P and U.S. Bellows to see technical details of past projects where products are made from an extensive range of materials.
The following are some of the key material choices that can be used to optimize cost and performance on your next project:
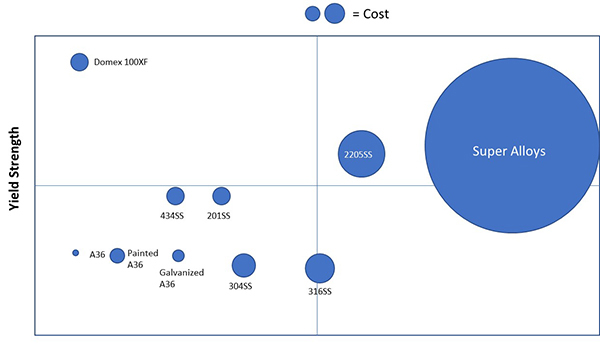
A36 Carbon Steel – this is the most common carbon steel. The major advantage is that it is widely available and even the most basic steel fabricator can work with A36.
High Strength Steel – there are many grades of the high strength steel that offer yield strength well beyond the 36 KSI offered by standard A36. Historically, manufacturers achieved higher strength with methods such as quenching and tempering. The disadvantage was that this caused the steel to be very difficult to form, bend, and weld. The automotive industry has led the charge for finding methods to produce stronger steels which also have excellent weldability and formability. Many steel manufacturers are working in the Automotive High Strength Steel 3.0 (AHSS 3.0) initiative to provide steels that have the holy grail of extreme strength, weldability, and formability. An example of this type of steel used by PT&P is Domex 100XF. This steel has a yield strength of 100 KSI or nearly 3x the strength of A36 while also having excellent weldability and bending characteristics.
Painted Carbon Steel – paint is a simple barrier protection. It is valued by some for its cosmetics when “fresh” from the factory. However, once the surface layer of paint is breached it offers limited protection to the underlying steel.
Galvanized Carbon Steel – the galvanizing process adds a layer of zinc over carbon steel that provides numerous advantages in terms of protecting the underlying steel. Unlike paint, the zinc is chemically bonded to the steel and will provide a far superior life vs paint in most applications with benefits such as cathodic protection of the underlying steel. View Technical Bulletin: Paint vs Hot-Dipped Galvanize
Stainless Steel – There are 57 standard grades of stainless steel as well as many proprietary grades such as Thermak 17 (AK Steel) and LDX 3201 (Outokumpu). All stainless steel contains 10.5%+ Chromium while leads to the formation of a passive oxide layer on the outside of the steel which protects it from corrosion. There are many additives such as nickel and manganese which can be used to modify the properties of stainless to achieve various desired outcomes in terms of cost, strength, corrosion resistance, etc.
View Stainless Steel Selection
Nickel Based Super Alloys – there are a wide variety of nickel-based superalloys that offer superior corrosion, chemical resistance, and performance at elevated temperatures versus stainless steel.