PT&P has been working with power plants since the mid-1970s and has deep expertise in the evolution of power plant design over the last 40+ years, including the impact that it has had on Pipe Stress Engineering requirements. PT&P has supplied products and services for a wide variety of power plants including Coal, Natural Gas, Biomass, Solar, Wind, Geothermal, Nuclear, and Hydroelectric. We have deep experience with the unique challenges of the key areas of most power plants. As the only major Global Provider of Expansion Joints, Engineered Pipe Supports, and Pipe Stress Engineering, we have the ability to provide unique solutions and solve the most difficult Piping problems. Some of our past jobs for power plants can be found in our featured product of the week archives including the below articles:
- Horizontal U-Type Constants for Power Plant
- Custom Variable Springs for Power Plant
- G-Type Constant Spring Supports Designed for a Power Plant in Mississippi
- Constant Spring Supports Designed for a Power Plant in New Mexico
- Hydraulic Snubber Assemblies Designed for a Geothermal Power Plant
- 60″ Dia. Elbow Pressure Balanced Expansion Joint for a Power Plant in California
Power Plants have unique requirements and even have a separate set of standards under B31.1. For example, annual Pipe Support inspections are required under B31.1 for power plants. One of the key differences with Power Plants is that they are designed around the conversion of energy from heat to electricity whereas many of our other plant customers are focused on a chemical process to create specific physical products/chemicals. Some of the unique challenges this leads to include:
- B31.1 requires annual inspections of Pipe supports
- Power Plants do not typically have Difficult Media
- Key processes reach 1000F+ with High Pressure making management of Pipe Stress critical
- Extensive use of steam requires proper management of Piping to avoid Steam Hammers
- Maintenance of Springs and Expansion Joints is critical to avoid thermal stress causing maintenance issues on expensive equipment – turbines, compressors, …
- Geothermal plants are uniquely challenging with a very high wear rate on piping
- Many power plants do not have the scale to allow for engineering personnel who specialize in Piping
- Peaker plants require more careful management of Thermal Stress as a large number of cycles can lead to Piping Failures
- Nuclear power plants have extremely stringent requirements and require specific certifications for most Piping components
- Coal-fired plants are, in some cases, viewed as not long term so are typically running under extremely tight budgets
Our product line for Power Plants include:
- Expansion Joints – Metallic, Fabric, and Rubber
- Spring Supports – Variables, Constants, Compact Disc Springs
- Dynamic Supports – Snubbers, Struts, Sway Braces
- Static Supports – Pipe Shoes, Pipe Saddles, Pipe Hangers, …
- Pre-Insulated Supports – Hot and Cold Applications
- Vibration Solutions – Stiffening, Dampening, and Isolation solutions
- Contact Corrosion Solutions – TPI, FRP, Slide Plates, Custom Designs
- Pipe Stress Engineering, Piping Design
- Field Service – B31.1 Inspections, Installation, Maintenance
The pictures below are just a sample of the custom solutions we have provided to different Power Plants over the years. PT&P has performed field service work in over 41 countries over the last 41 years.
Below is a sample of the engineering and field service work we have done for power plants. Previous projects have included:
- Pipe Stress Engineering
- Pipe Support Design
- Computational Fluid Dynamics
- Inspection/Installation
- Vibration issue identification and resolution
- Emergency Service
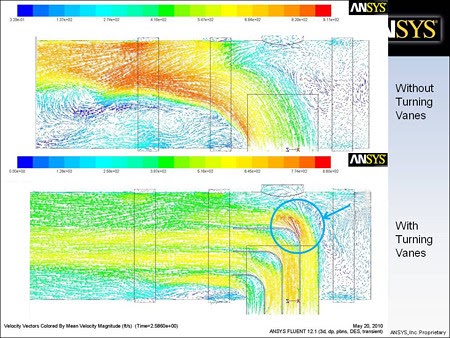
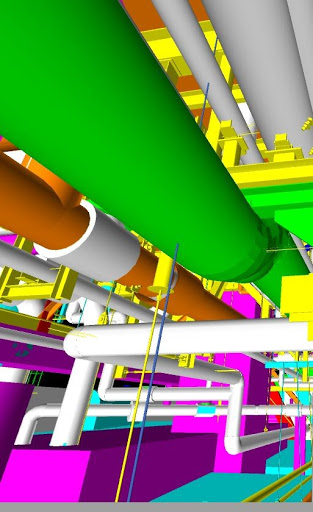
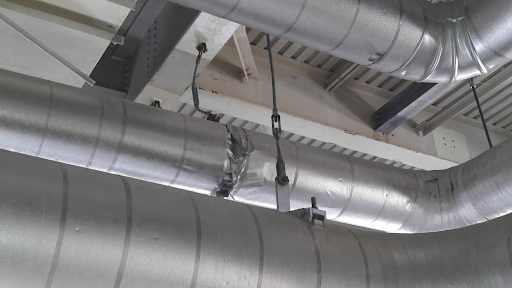
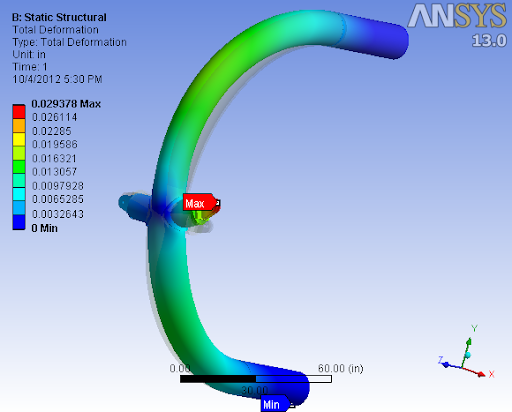
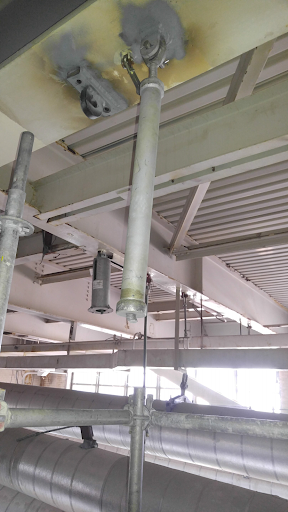
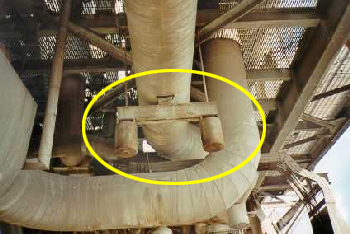
Boilers:
Boilers are critical to most power plants. Most use supercritical power boilers, where the steam and pressure reach temperature 600℃, and pressure is over 3200 PSI. This allows greater efficiency in driving steam turbines to generate electricity. The challenge is that the temperature can drive 8+ inches of thermal growth in 100 ft of carbon steel and 10+ inches in stainless steel or nickel-based superalloys in addition to the challenges posed with extremely high pressure.
Some of the Key Components that PT&P has supplied in Boiler include:
- Furnace Springs – typically these are constant spring hangers. PT&P has launched the Nano-Constant, which is the smallest constant available, in order to accommodate situations with difficult space limitations.
- Expansion Joints – these are typically used in the exhaust piping
- Snubbers, Sway Braces, Struts – dynamic restraints are used in boiler applications as a safety measure against an external or transient event: seismic, steam hammer, etc.
Examples of Our Products:
|
Heat Recovery Steam Generator (HRSG):
Heat Recovery Steam Generators (HRSGs) are generally used as a thermodynamic link between two sets of turbines: a combustion turbine and a steam-powered turbine in combined-cycle natural gas-fired power plants. The combustion turbine generates electricity independent of the rest of the system, but the excess heat in the exhaust gas from this turbine means that not all of the natural gas’s potential energy has been captured. Plants use HRSGs to harness the remaining energy in the exhaust gas, increasing the conversion efficiency of the fuel’s energy into electricity. The HRSG runs the hot exhaust gas past thin lines of water, transferring the heat to the cooler water, which is turned to steam. As this steam builds up, it is routed to a steam turbine where the pressure and temperature of the steam push it through a turbine, spinning it and generating electricity as the steam makes its way to an area of lower pressure and temperature. This process can make gas-fired combined cycle plants around 50% more efficient than gas-fired single-cycle plants as more of the fuel’s chemical potential energy is captured by the HRSG system. HRSGs operate at high-temperature and pressure. The exhaust itself can reach up to 1,300℉ while the steam reaches temperatures of up to 1,200℉ and pressure of up to 200 Bar.
![]() |
Below are pictures of a few of the products we have supplied for HRSGs over the years. With elevated temperatures and pressure, HRSGs have some of the same dynamics as Boilers but are not combusting fuel to generate energy.
Turbines:
Turbines have multiple functions in different types of power plants. They can be designed for steam- or combustion-powered electrical generation. Combustion turbines often serve as the primary method of transforming the fuel (typically natural gas or other liquid fuels) into mechanical and then electrical energy. Steam turbines are often secondary in the power-generation process because the steam must first be heated by the fuel’s combustion (boilers) or the exhaust gas (HRSG). In both turbines, the gases (steam or combustion gas) are forced through the turbine blades because of their high pressure and temperature, which spins the turbine (mechanical energy). Gas flowing through the combustion turbines can get as hot as 2,300℉. However, some of the turbine’s critical metals can only withstand up to 1700℉, so cooler air from the compressor can prevent key components from overheating. In steam turbines, typical inlet temperatures are around 1,050℉, and pressure is around 150 Bar. The turbine relies on highly sophisticated blade designs to utilize the energy of the gas or steam to turn a shaft.
Management of thermal stress is critical for Turbines as they are very expensive as well as highly sensitive to excess stress. In addition, the temperature and pressure on the inlet side of the turbine limit options while also leading to larger degrees of thermal growth. The pictures below are a few of the many products we have supplied for applications in the Turbine lines.
If you would like to discuss this further, call and speak with one of our expert engineers at 713-731-0030.