Frequently Asked Questions
This decision would be made by a pigging services company during the design process. Technical data and financial impacts would have to be analyzed prior to choosing whether or not a pig launcher and receiver should be combined. We fabricate the products according to the specifications provided to us after the analysis is complete.
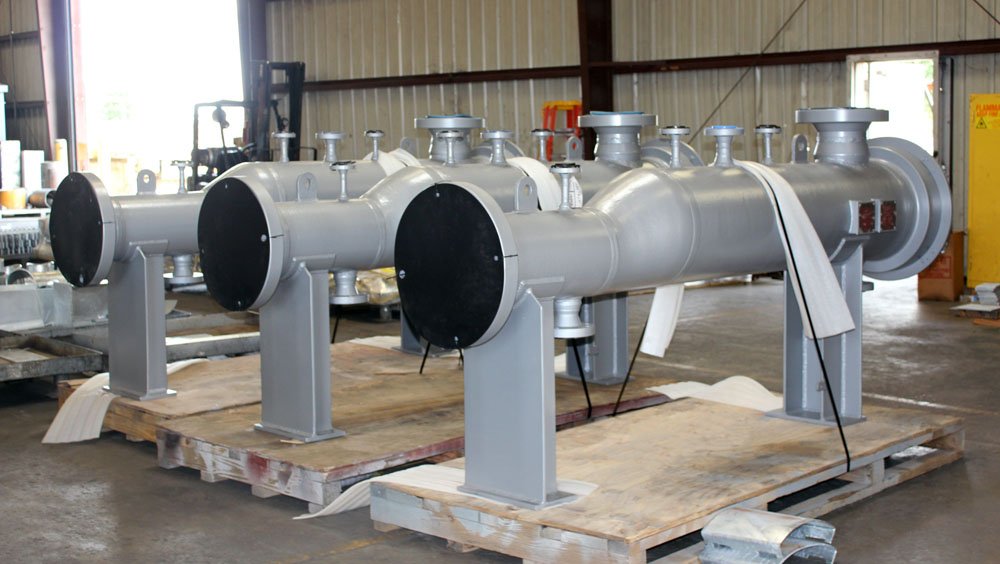
Pig Launchers and Receivers
We design the davits and have developed a standard design for ones that are generally 12”-24” in size. We design each davit per requirement for sizes above 24”.
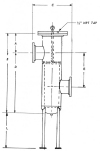
Standard Design Part C
Elevation with blind flange. Davit Assembly
(optional)
Normally, we only use ASME Codes to evaluate reduction of thickness in pressure vessels.

Pressure Vessel (Process Feed Tank)
A major barrel is bigger than the normal piping in the system to make it easier to insert the pig and launch and receive it. The minor barrel has the same inside diameter as the main pipeline and is used to clean the pipes.
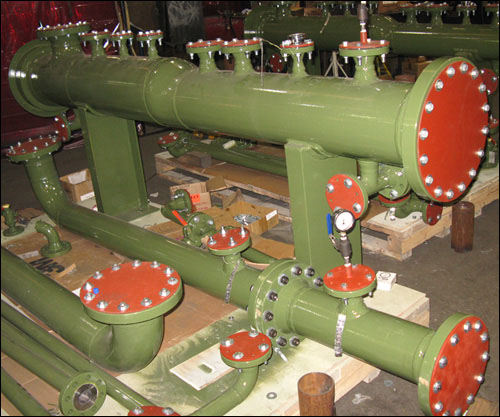
Pig Launchers and Receivers with Safety Locking System
( 675 psig at 200°F)
Hydro-test pressure and holding times vary for different design codes. For example, the ASME SEC VIII Div.1 general hydro-test pressure will be1.3 x design pressure (minor factors may vary for this equation as well) and for piping design codes, the hydro-test pressure will be ASME B31.4,B31.8 1.5 x design pressure.
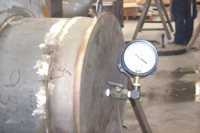
Bellows of an expansion joint going through a hydro-test pressure.
A davit (particularly for man ways) is a mechanically designed hinged guide and support system that helps ease the opening and closing of large and heavy blind flanges. This assembly can be designed for horizontal and vertical applications.

B Standard Design Type
Elevation with Davit Assembly
A spectacle blind consists of a blind and spacer. The blind is installed in between flanges to securely shutdown pipeline during leakage or maintenance. When a blind is not required, a spacer can be installed in between flanges to continue regular operating conditions.
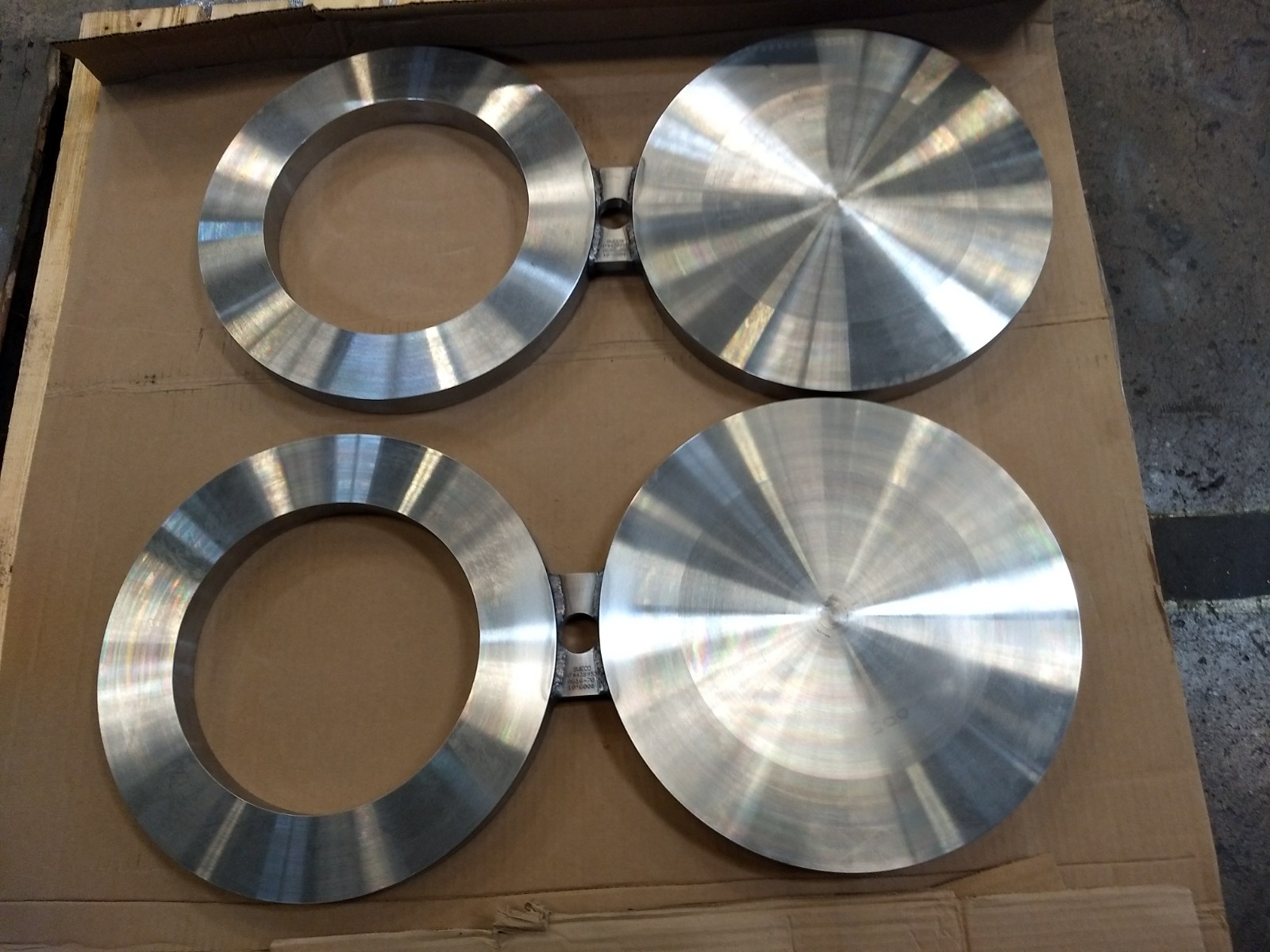
Spectacle Blinds
The flow rate is the amount of liquid passing through a particular area over a period of time. It is generally measured in gallons per a minute or cubic feet per meter.

Orifice Plates
The small hole on orifice plates restricts flow which causes the pressure to drop. The pressure can be measured using pressure gauges before and after the orifice plates which allows you to determine the flow rate using the Bernoulli’s Equation. An orifice plate is installed between orifice flanges or a metering unit.

Orifice Plates
An orifice plate is a device used for measuring flow rate. It is a thin plate with a hole in the middle that is usually placed in a pipe where fluid flows.
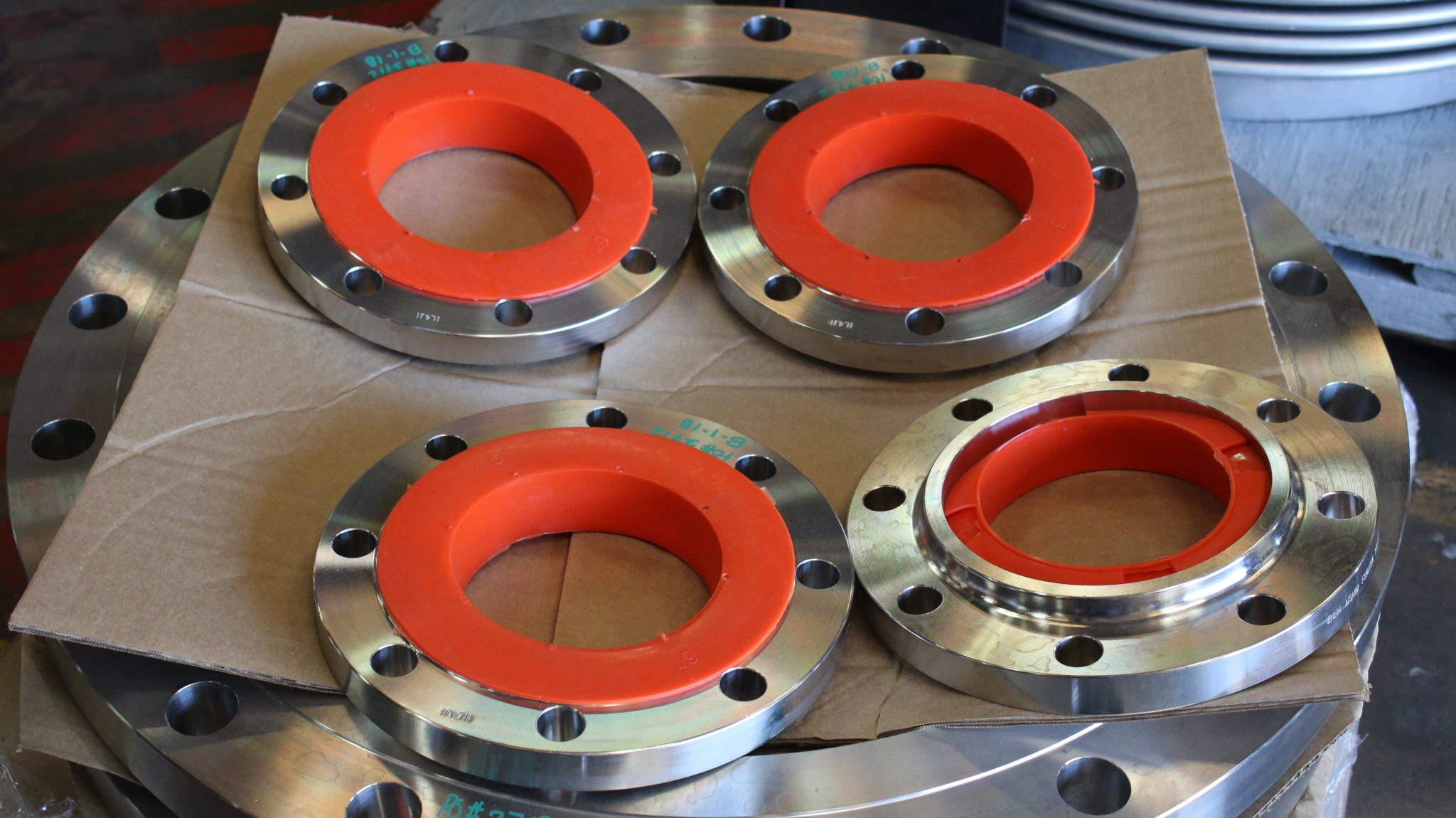
Orifice Plates
Media that can pass through a transition piece include air, liquid, gasses, dust, dirt, and chemicals.

159″ Long x 60″ Wide Transition Piece
Duct work assemblies can include fabricated elbows, tees, straight sections of duct work, fabric or metallic expansion joints and can be rectangular or round.

60″ Diameter Carbon Steel Duct Work/p>
Ducts are a series of sectioned tubes, which transfer either heated or cooled air from the furnace or air conditioner, throughout the building.
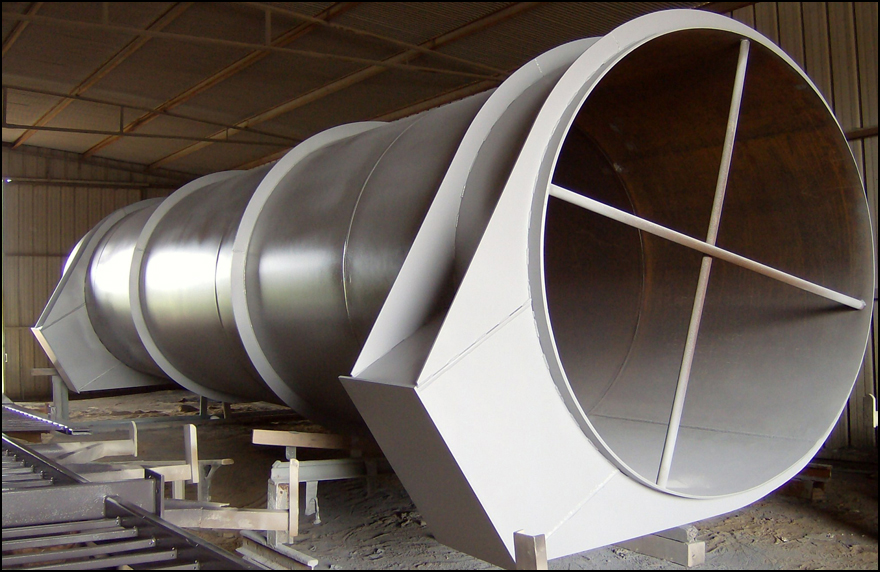
90″ Diameter Duct Work
Dampers can be manually operated or motor-driven.
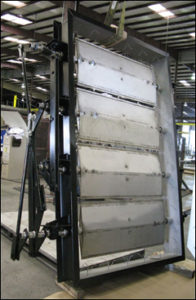
Damper
Sweco Fab, Inc., our subsidiary, holds the National Board R-Stamp which enables us to do repairs and alterations on pressure vessels, boilers, and pressure-retaining items. Sweco acquired the National Board R-stamp in 2007. The R-Stamp requires maintaining high standards in materials, systems, and procedures and is issued by the National Board of Boiler and Pressure Vessel Inspectors.

Pressure Vessel Manufactured by our Subsidiary, Sweco Fab
Sweco Fab, Inc., our subsidiary, holds the ASME U-Stamp which gives us the ability to manufacture and work on unfired pressure vessels. Sweco acquired the ASME U-stamp in 1962 and has maintained it through-out the regular audits. The U-Stamp represents ASME's section VIII Division 1; rules for the construction of pressure vessels. In order to obtain the U-Stamp, Sweco Fab was required to meet ASME's guidelines for the design, fabrication, inspection, and testing of Pressure Vessels. In order to maintain the U-stamp, we regularly update our designs and fabrication processes while undergoing routine examinations and inspections.

Pressure Vessel Manufactured by Sweco Fab
We use CAESAR II software to conduct pipe stress analysis on duct systems.
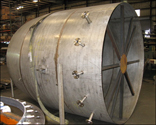
96″ Diameter Stainless Steel Duct Work