Stainless Steel
There are 57 standard grades of stainless steel in addition to many proprietary grades that are manufacturer specific. The 3 major types of Stainless Steel, Austenitic, Ferritic, and Martensitic are defined based on their crystalline structure:
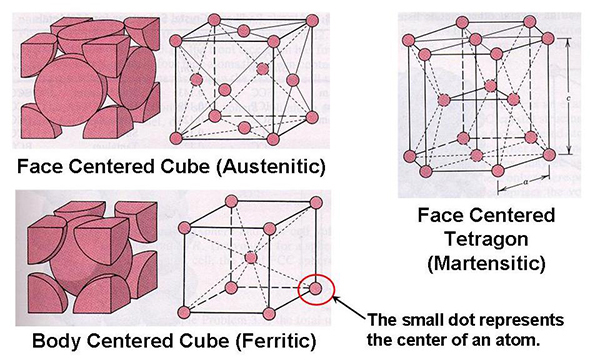
Ferritic – these stainless steels have a body-centered crystalline structure. They are not as corrosion-resistant or weldable and formable as Austenitic stainless steel. However, they do tend to have higher strength. 400 series stainless steel is Ferritic.
Austenitic – these stainless steel have a face-centered crystalline structure. Nickel (or in some cases Manganese) is added to stabilize the austenitic crystalline structure. Beyond superior weldability and formability, these stainless steel perform much better in cryogenic applications whereas ferritic stainless steel becomes very brittle at Cryogenic temperatures. 200 and 300 series stainless steel are austenitic.
Duplex – these stainless steel combine the properties of Duplex and Austenitic. The major advantage is that they have the workability and corrosion resistance characteristics of Austenitic and the higher strength of ferritic stainless steel. 2000 series stainless steel is Duplex. Types of Duplex are characterized into Lean, Regular, and Super. The biggest difference is in the level of Nickel and Chromium content as well as some other specialty items that are added with the tradeoff being cost versus corrosion performance.
Martensitic – these stainless steel have a body-centered tetragonal structure.
The table below shows the key elements used in Stainless Steel beyond iron:
Many fabricators and engineering firms will focus solely on 304 and 316 stainless due to limitations in their own capabilities. This misses the potential for optimization of cost and performance in some applications. The chart below shows just a partial listing of stainless steel and the tradeoffs on corrosion resistance, strength, and cost. Utilizing the full range of stainless steel requires more engineering and manufacturing skills but can pay dividends in the right application. PT&P works directly with some Stainless Steel Manufacturers for recommendations on optimal choices for a given application.
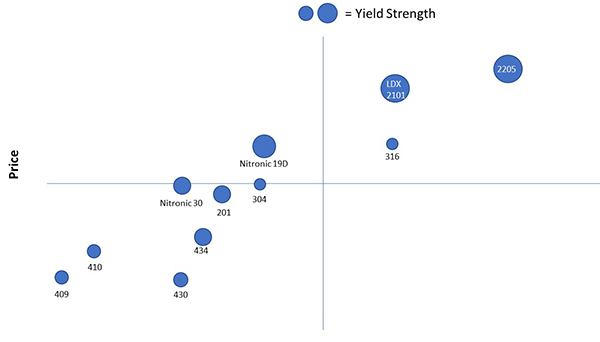