INSTALLATION OF HYDRAULIC SNUBBERS:
STEP 1: Check that front paddle is securely fastened to the piston rod. If loose, tighten the connection by means of holding the piston rod on the wrench flats provided and tightening the paddle against it. DO NOT use a pipe wrench on the chromed shaft of the rod. Try to minimize the amount of rotation of the piston rod within the cylinder to prevent possible scoring or seal damage. Torque the connection to between 15 and 25 ft-lb. for all cylinder sizes.
STEP 2: If required, attached the extension piece to the rear of the cylinder or check the torque of the nuts if already assembled. Note: When tightening the extension piece nuts, use a wrench on the tie-rod nuts at the piston rod end of the cylinder to apply a counter-torque. If this procedure is not followed, the cylinder tie rods will loosen. Torque the nuts to the valves listed in the chart below.
|
STEP 3: Consult the hanger detail to determine the required as-built cold pin-to-pin dimension. The extension piece comes equipped with a threaded rod connection to accommodate field length adjustments. Sight holes are provided in the extension pipe to ensure proper thread engagement. The male threads must be visible through these holes for proper load carrying capability. A lock nut is provided to freeze the adjustment. Torque to 50 ft-lb. for all cylinder sizes. For hanger assemblies not equipped with extension pieces (FIG. 510 AD) field length adjustment must be accomplished by repositioning the supporting structures or the cylinder cold set. Approval of new cold set by Shaw FCI should be obtained. Refer to Section E for this procedure.
STEP 4: Orient each end attachment or pipe clamp to ensure that the available alignment provided by the ball bushings is within the allowed 10 degree cone of action.
STEP 5: Hoist the assembly into place. Cylinders equipped with remote reservoirs can have the reservoir de-coupled at this time provided it will not be necessary to reposition the cylinder piston rod during installation. Reconnect the reservoir after the assembly has been pinned in place. NOTE: Due to the pressurized design of Shaw FCI reservoirs, there is no concern for orientation as it will function properly in any spatial orientation. It is recommended that the elevation of the remote reservoir be at or above that of the main cylinder.
The load pins provided with the assembly fit into close tolerance holes for which care must be exercised during installation. Removal and insertion should be accomplished carefully and without undue force. Spacer washers are provided to ensure proper function of the ball bushing alignment feature. The load pins are provided with cotter pins which must be securely installed. Any relocation of the assembly to clear an interference should be brought to the attention of the project engineer. Adherence to project tolerance guidelines should be observed.
STEP 6: Remove and discard the piston rod locking clamp (if supplied). Recheck all bolted connections. For units supplied with remote reservoirs, ensure that proper connections are made and that the flexible hose is free from kinks. Visually examine the entire assembly for erection damage, paying particular attention to the chromed surface of the piston rod. This completes the installation of the assembly.
To Maintain Hydraulic Snubbers
Under normal operating conditions hydraulic snubbers are maintenance free. In severe service (usually involving excessive vibration or high temperatures) the seals may become damaged, causing a loss of fluid. In this case the snubber must be completely disassembled, new seals must be installed, and the snubber must be refilled with fluid.
INSTALLATION OF MECHANICAL SNUBBERS
First, the snubber must be set at the cold position. Under normal operations, the snubber will extend in the positive direction from the initial (cold) position to the operating (hot) position. In rare installations, the snubber may be expected to move in the negative direction by some known amount. The cold position must be set so that the snubber will never closer than ½ to 1 in from the end of its stroke. In most cases, this means that the cold setting will be ½ to 1 in from one end of its stroke range. At the operating conditions the snubber should have at least 1 in of possible travel.The snubber should be installed with its axis parallel to the direction of expected impulsive load. This may or may not be the direction of thermal movement. If the two movements are not in the same direction, there are some additional installation considerations. In this case the snubber should normally be ordered with ball joints at both ends, as shown in the diagram below. The snubber should be mounted so that the major expected thermal movement is in the plane of the ball joints.The overall length is adjustable from 2″ to 6″ by means of the threaded rod on the extension end of the unit.
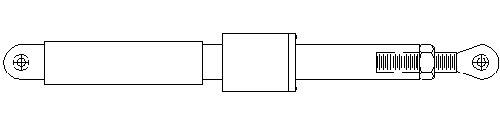
CAUTION: Do not use the piston side threaded rod end for adjustment. Full thread engagement is critical for safe operation.
To Install Mechanical Snubbers
1. Determine the direction and magnitude of thermal motion and impulse load.Adjust the snubber so that after the thermal expansion, the snubber will be in the middle of its travel range. Temporarily install unit in the operating position. Tack weld end brackets to the fixed structure and to the pipe that it is to control. For units furnished with a pipe clamp connection, install the clamp at this time. (CAUTION: Do Not Allow Weld Spatter To Contact Snubber Unit). After tack welding, remove pivot pins from both ends of the snubber assembly, set the unit aside and complete welding. Tighten pipe clamp bolts if applicable. Reinstall snubber assembly between end brackets and replace pivot pins and cotters.
2. Installation is now complete, and the snubber assembly is ready for operation.