EDI stands for Electronic Data Interchange. PT&P regularly conducts electronic data interchange with customers. We dedicate an in-house team of software developers and integrators to setup intra-company electronic processes that increase data accuracy and reduce cycle time.
Tag: technology
April 2004 News
Updated Version of PHDS Download
Pipe Hanger Design Software (PHDS) is an easy-to-use program that allows you to easily generate CAD drawings of PT&P’s variables, constants, and rod hanger supports together with a complete bill of material. You may also send the drawings to info@pipingtech.com or 1+713-731-8640 (fax) for an immediate quote.
PHDS Software
Software Features
- Generate 2D drawings of variable, constant, and rod hanger pipe supports from a large selection of pre-defined assemblies Save drawings as .dwg filesUse an Excel datasheet to generate drawings in batch mode Add a location plan to the drawings in PHDS or through the Excel datasheetGenerate drawings in either FPS, Metric, or SI units
- Use a built-in function to submit drawing data to PT&P for quotation
March 2002 News
PT&P Utilizes 3D-Modeling Technology to Design Pipe Supports for a 750MW Power Plant
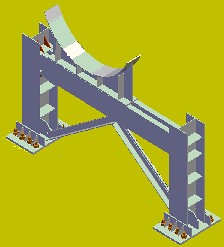
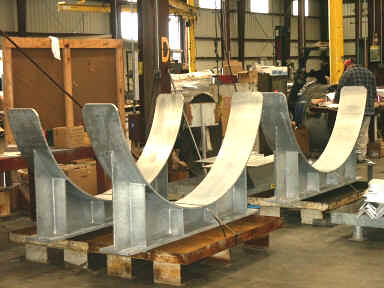
Piping Technology & Products, Inc. recently designed and fabricated 9 pipe supports with loads up to 75,000 lbs. for a 750MW power plant in Alabama. After extensive engineering hours and structure analysis, PT&P’s engineering department produced a detailed design and 3-D model for the supports that would allow them to run electronic interface checks. The supports are to support the cooling towers’ circulatory water system at the power plant. Six of the 9 supports were designed for a 60” line and 50,000 lb. load, and the remaining 3 were designed for a 78” line and 75,000 lbs. of load.
Furnace Springs Versus Standard Springs The major differences between standard springs and furnace springs are their construction and intended use. Furnace springs operate in much the same way as other variable spring supports. They are designed to support the pipe and tubes that are subject to vertical thermal movement. The design changes come about because, furnace springs are exposed to extreme temperatures.
|
August 2001 News
Breaking News: NEW pipingtech.com
On August 06, 2001, PT&P launched its new website. pipingtech.com now has a new design and structure. We hope you will find it simpler and more intuitive to find what you are searching for. Browse through its many pages and explore the new features that we have added:
Features:
- Menu bar with mouse over features. Allows you to view the different categories under that section before you click on it.
- In the news side menu bar- Allows you to view and select PT&P’s current press releases
- A new products section that is categorized by type of product.
- Product testing section – Describes the type of testing we do, the procedure and its purpose
- Highlights section – Highlights upcoming events, stories, additions, etc.
- Emergency/Quick Turn Request Form
- Easily accessible catalog request form
Improved Hydraulic Snubber in Final Stages of Development
PT&P has been developing and testing a better hydraulic snubber during recent months. Final independent tests at a university laboratory are confirming our tests.
PT&P’s new snubber design features a spring-loaded cylinder in the hydraulic reservoir which feeds the main cylinder. This design is more compact, and it allows the snubber to be mounted in any orientation. With the addition of test equipment from our recent acquisition from the Basic Engineers Auction, PT&P plans to have these snubbers in production by the end of this year.
3D Models of PT&P Spring Hangers and Hardware are now available for Intergraph’s PDS Plant Design Software.
Do you want more information about hydraulic snubbers? Visit our webinar archives today!
Figure Conversion Chart on the Web
PT&P’s World Wide Web site will soon host another valuable technical resource for engineers around the world. A figure number conversion tool will allow engineers to enter alternative figure numbers (Grinnell and others) and find matching PT&P figure numbers.Engineers are encouraged to replace alternative figure numbers with corresponding PT&P figure numbers in their technical specifications. Look for the PT&P Figure Conversion Tool online at our web site.
PT&P Collaborates on PDS Software
Piping Technology & Products is collaborating with other sponsors to create a pipe support module for an industry leading plant design software package, PDS. The concept for the pipe support module was developed by another company, and PT&P became involved in August 1997.
Programming has been added which will enable users of PDS to easily integrate PT&P pipe supports and hardware components with their PDS models. To prepare for the project, PT&P has participated in 4 weeks of training at Intergraph’s site in Huntsville, AL learning the PDS system and the EDEN programming language.
PT&P Facts
“Like a Rock” Polyurethane Blocks
Chevrolet uses the phrase “Like a Rock” to advertise their pick-up trucks. PT&P recently produced some polyurethane blocks for a major E&C customer to their specification of 2,000 pound compressive strength as measured by ASTM D1621 tests. Our supplier produced a special chemical blend for a nominal density of 38 pounds/cubic foot and PT&P built special molds to satisfy this “Like a Rock” requirement for the Gulf Coast ethylene plant.
PT&P Technical Team Goes to Algeria
In March, PT&P sent a technical team to a LNG facility near Skikda, Algeria to provide assistance on pipe support replacement for the GL1K project. This large facility has several units that have operated for more than twenty years. Our team examined the units and recommended replacement of cryogenic and spring supports. Since travel in Algeria is subject to heavy restriction, our team had to fly from Tarbarka, Tunisia by helicopter to and from the job site. The trip lasted about two weeks.
Advancements at PT&P
The newest addition to the Piping Technology & Products, Inc. family of machinery is a thermal spraying unit used for coating touch-ups on our equipment. The versatility of this piece of equipment makes it possible to recoat small areas of our products (which may have been missed by galvanizing) and ship them out quickly, without having to spend the time necessary to send the product for a completely new galvanizing job.
The spray gun works on a relatively simple principle. An electric arc within the gun melts the coating material, which is fed into the gun in wire form. As the wire feeder pulls the wire into the high heat zone, it is melted and blown or sprayed onto the surface to be coated by a forceful stream of compressed air. The spray coats the surface and cools to form a strong, flat structure which will protect the given material.
We at PT&P are very excited about this new addition to our shop, and are pleased that it will certainly allow us to offer you quicker deliveries and lower cost in the long run.
New Spirit of Excellence as PT&P Implements Bar-coding Plan for Quality

This fall, in the spirit of total quality, Piping Technology is beginning the implementation of a brand-new bar-coding system to streamline shipping, improve inventory techniques and maximize efficiency in all facets of our operation. The effects of this system will certainly be far-reaching, and will undoubtedly affect our customers positively and for years to come.
At present, the bar-coding system seeks to make shipment of jobs easier for both PT&P and for our clients around the world. All products are labeled with a computer-generated tag before they go out, thus cutting down on errors and man-hours, while simultaneously improving the readability and appearance of shipped products. See below for an example of our new shipping tags. As technology improves all around, we also expect for barcode scanners to be used by us and our clients. The scanners will allow for an instantaneous electronic record of all transactions to be made by whomever operates them. In this way, speed and efficiency will be running at peak levels on all sides.
Fuel Cell Technology: PT&P's Role in Tomorrow's Energy Production
PT&P has received a contract to design, develop and furnish all of the supporting systems for a 250 kW fuel cell unit prototype. Greg P. Michaels and Kishor Bhalara represented PT&P in this venture, designing the alloy supports for the piping and equipment. See below for a look at the fuel cell. PT&P’s contributions are shown in dark green.
Fuel cell technology is a cutting-edge advance in the field of energy production. Though in principle fuel cells have been in development for over 150 years, today’s refinements and prototypes have put the units closer to commercial availability than ever before. During the “space race” of the 1950s and 1960s, NASA launched fuel cells into space for electrical generation on its Gemini and Apollo missions. Today, they are regularly used in space shuttle missions. Until recently, the high cost of fuel cells made them prohibitively expensive for commercial use. However, experts are now predicting a drop in the price per fuel cell kilowatt, and have even ventured that as much as 60,000 MW of power will be produced by fuel cell in the year 2010.
The fuel cell works on a simple though significant principle. Fuel cells produce power by converting chemical energy directly into electrical energy, without requiring work like that done by a rotating generator. As the need for mechanical work is eliminated, the efficiency of the fuel cell increases dramatically. If a fuel cell takes advantage of cogeneration technology as well, the overall efficiency of the unit skyrockets to between 80 and 90 percent, unheard of in conventional power generation schemes. See the diagram below for a look at PT&P’s contributions to this revolutionary advance in energy production technology.
Piping Technology and Products, Inc. is thrilled to be a part of this piece of history. This prototype is certain to profoundly affect the way the world gets its power in the future. PT&P continues to look toward the twenty-first century in our quest for innovation and excellence.